Custom Rubber Patches & Labels Tailored to Your Needs.
-
Material Types: PVC, Silicone, TPU
-
Design and Structure: 2D, 3D, Embossed (raised), Debossed (recessed), Custom shapes, Custom sizes, Variable thickness
-
Color Options: Full color, Transparent, Glow-in-the-dark, UV-reactive
-
Attachment Methods: Sew-on, Heat-seal, Adhesive backing, Velcro
-
Durability Features: Waterproof, UV-resistant, Heat-resistant, Stretchable (Silicone), Outdoor-use durability
-
Special Features: Glow-in-the-dark, Eco-friendly materials (Silicone)
-
Finishes: Matte, Glossy, Textured finishes


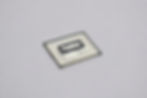


What are PVC patches?
PVC patches, short for Polyvinyl Chloride patches, are versatile and durable custom embellishments for clothing and accessories. Manufacturers create these 3D patches by molding soft PVC material into intricate designs, logos, or text. The process allows for vibrant colors and detailed textures, making PVC patches popular for military patches, brand logos, and promotional items.
Custom PVC patches offer several advantages:
-
Durability: PVC resists wear, tear, and fading, even in harsh conditions.
-
Flexibility: The material conforms to fabric contours, enhancing comfort.
-
Detail: PVC captures fine lines and complex designs with precision.
-
Waterproof: These patches withstand moisture, making them ideal for outdoor gear.
-
Customization: Designers can incorporate multiple colors and raised elements.
While PVC patches excel in many areas, they're just one type of custom rubber patch. TPU and silicone patches offer alternative characteristics that might better suit specific project needs.
What are TPU patches?
TPU patches, made from Thermoplastic Polyurethane, represent a modern alternative in custom patch manufacturing. These flexible, durable emblems offer unique benefits for clothing brands and apparel manufacturers seeking high-quality customization options.
Key features of TPU patches include:
-
Elasticity: TPU material stretches and recovers, conforming to fabric movement.
-
Lightweight: These patches add minimal bulk to garments, maintaining comfort.
-
Abrasion resistance: TPU withstands repeated wear and washing cycles.
-
Eco-friendly potential: Some TPU formulations offer biodegradable options.
-
Heat resistance: TPU patches maintain their integrity in high temperatures.
Custom TPU patches excel in applications requiring softness and flexibility. Sportswear brands often choose TPU for its ability to move with athletic gear without compromising durability. The material's pliability also makes it ideal for creating 3D rubber patches with subtle raised elements.
Manufacturers produce TPU patches through injection molding or heat pressing, allowing for intricate designs and vibrant colors. The versatility of TPU enables the creation of both simple logos and complex, multi-colored emblems.
What are silicone patches?
Silicone patches represent a premium option in the custom patch market, offering unique properties that set them apart from PVC and TPU alternatives. These soft rubber patches deliver a combination of durability, flexibility, and heat resistance that makes them ideal for high-end apparel and specialized applications.
Key characteristics of silicone patches include:
-
Extreme flexibility: Silicone bends and stretches without cracking or losing shape.
-
Heat tolerance: These patches withstand high temperatures, making them suitable for iron-on application and heat press customization.
-
Chemical resistance: Silicone repels oils, solvents, and many harsh chemicals.
-
Hypoallergenic properties: Ideal for sensitive skin and medical-grade applications.
-
Vibrant color retention: Silicone maintains its appearance even after repeated washing.
Custom silicone patches offer clothing brands a luxurious feel and appearance. The material's pliability allows for the creation of intricate 3D designs with multiple layers and textures. This makes silicone patches particularly popular for high-end sportswear, outdoor gear, and fashion accessories.
Manufacturers produce silicone patches through injection molding or casting processes. These methods enable the incorporation of fine details, gradients, and even translucent elements in patch designs.
What are the differences between PVC, TPU, and silicone patches?
PVC, TPU, and silicone patches each offer unique characteristics that cater to different needs in custom patch manufacturing. Understanding these differences helps clothing brands and garment producers choose the ideal material for their specific applications.
Texture and Feel
-
PVC patches have a firm, slightly rigid texture with a glossy finish.
-
TPU patches offer a softer, more pliable feel with a matte or semi-gloss appearance.
-
Silicone patches provide the most flexible and rubber-like texture, often with a smooth, velvety surface.
Durability
-
PVC excels in overall durability and weather resistance.
-
TPU offers superior abrasion resistance and elasticity.
-
Silicone provides the best heat resistance and maintains flexibility in extreme temperatures.
Environmental Impact
-
PVC raises some environmental concerns due to its chlorine content.
-
TPU offers more eco-friendly options, with some biodegradable formulations available.
-
Silicone, while not biodegradable, is inert and generally considered safe for the environment.
Application Methods
-
Manufacturers commonly sew PVC patches or attach them with adhesive.
-
TPU patches allow for heat pressing and sewing applications.
-
Silicone patches offer versatility in attachment, including sewing, adhesive, and heat pressing.
Design Capabilities:
-
All three materials allow for detailed designs and multiple colors.
-
PVC and silicone excel in creating pronounced 3D effects.
-
TPU offers the best balance between detail and softness for 3D rubber patches.
By weighing these factors, brands can select the optimal material for their custom patches, ensuring the perfect blend of aesthetics, functionality, and cost-effectiveness for their products.
How durable are these patches?
PVC, TPU, and silicone patches all offer exceptional durability, making them ideal for long-lasting garment embellishments. However, each material exhibits unique strengths in different aspects of durability:
Wear Resistance:
-
PVC patches excel in resisting daily wear and tear.
-
TPU offers superior abrasion resistance, maintaining appearance even with frequent use.
-
Silicone patches provide the best flexibility, preventing cracking or peeling during movement.
Washing Durability:
-
All three patch types withstand multiple wash cycles.
-
PVC maintains color vibrancy even after numerous washes.
-
TPU and silicone patches retain their shape and texture better in machine washing.
Weather Resistance:
-
PVC patches offer excellent resistance to UV rays and moisture.
-
TPU provides good all-weather performance, especially in extreme temperatures.
-
Silicone excels in maintaining flexibility and appearance in varying weather conditions.
Chemical Resistance:
-
Silicone patches offer the best resistance to oils, solvents, and chemicals.
-
PVC and TPU also provide good chemical resistance, though not as comprehensive as silicone.
Heat Tolerance:
-
Silicone patches withstand the highest temperatures without deformation.
-
TPU offers good heat resistance, suitable for most applications.
-
PVC may soften at extremely high temperatures but remains durable in normal conditions.
Color Fastness:
-
All three materials maintain color well, with minimal fading over time.
-
PVC often shows the least color change, especially in outdoor applications.
Flexibility and Stretch:
-
Silicone patches offer the highest flexibility without cracking.
-
TPU provides good stretch recovery, ideal for athletic wear.
-
PVC, while less flexible, maintains its shape well over time.
Edge Durability:
-
PVC patches typically have the most durable edges, resisting fraying or peeling.
-
TPU and silicone edges may be more prone to wear but offer better overall flexibility.
The durability of these patches ensures they often outlast the garments they adorn. Proper care, such as following washing instructions and avoiding harsh chemical exposure, can further extend their lifespan. Clothing brands often choose patch materials based on the specific durability requirements of their target market and product line.
Can these labels be applied to different types of fabric?
Yes. PVC, TPU, and silicone patches offer versatility in fabric application, making them suitable for a wide range of garments and materials. Here's a breakdown of their compatibility with various fabrics:
Cotton and Cotton Blends:
-
All three patch types adhere well to cotton.
-
PVC patches provide excellent contrast on cotton fabrics.
-
TPU and silicone conform better to the natural stretch of cotton blends.
Synthetic Fabrics (Polyester, Nylon):
-
PVC, TPU, and silicone all bond effectively with synthetic materials.
-
TPU patches often perform best on moisture-wicking athletic wear.
-
Silicone patches offer superior flexibility for form-fitting synthetic garments.
Denim:
-
PVC patches create a strong, long-lasting bond on denim.
-
TPU and silicone options work well for stretchier denim blends.
Leather and Faux Leather:
-
Silicone patches adhere best to leather surfaces.
-
PVC can work with proper preparation and adhesive selection.
-
TPU offers a good balance of adherence and flexibility on leather items.
Stretchy Fabrics (Spandex, Lycra):
-
Silicone and TPU patches excel on highly elastic materials.
-
PVC may limit the stretch of these fabrics and is less commonly used.
Wool and Wool Blends:
-
PVC patches can work well on wool with proper attachment methods.
-
TPU and silicone offer better conformity to wool's texture.
Delicate Fabrics (Silk, Satin):
-
Silicone patches, being the softest, are often preferred for delicate materials.
-
Lightweight TPU patches can also work well.
-
PVC is generally avoided on very delicate fabrics.
When applying patches to different fabric types, consider these factors:
-
Fabric stretch: Choose flexible patch materials for stretchy fabrics.
-
Washing requirements: Ensure patch durability matches the garment's care instructions.
-
Fabric texture: Select patches that complement or enhance the fabric's natural feel.
-
Intended use: Match patch durability to the garment's purpose (e.g., workwear vs. fashion).
Clothing brands often conduct testing to ensure optimal patch performance on specific fabric types. Proper application techniques, such as heat pressing or specialized adhesives, play a crucial role in achieving the best results across various fabric types.
Disclaimer
The content appearing on this webpage is for informational purposes only. Bennson Label makes no representation or warranty of any kind, be it expressed or implied, as to the accuracy, completeness, or validity of the information. Any product specifications, design features, quality descriptions, or production processes mentioned should not be interpreted as guaranteed characteristics of the final delivered products. Customers are responsible for clearly defining their specific requirements when placing orders for custom labels, patches, tags, or any other accessories. The actual products may vary from descriptions or images shown. Please refer to our terms and conditions for more information on ordering, production, and delivery processes.
Author
Hasan Karaloglu
Hasan brings 6 years of expertise in garment branding and partnerships with over 20 elite fashion brands. His insights and experience drive Bennson Label's commitment to excellence and industry-leading solutions.
Share Your Details with Us
Please fill out the form with your project information, including volume and deadlines. This will allow us to offer the most accurate advice on how we can support your needs with our custom textile and packaging services.